
harnessing the power of co-production
Our breakthrough process delivers multiple market-ready industrial materials—starting with cement.
we start with a carbon-free feedstock
TRADITIONAL CEMENT RELIES ON LIMESTONE AS ITS CORE FEEDSTOCK, WHICH ACCOUNTS FOR 60% OF CEMENT'S TOTAL EMISSIONS.
The Brimstone process replaces limestone with highly abundant and carbon-free calcium silicate rocks, dramatically reducing our cement's carbon footprint from the start.
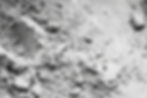
what is portland cement?
Portland cement has been the foundation of modern construction for over 200 years, comprising virtually the entire U.S. cement market. As the binding ingredient in concrete, portland cement is essential for building infrastructure like skyscrapers, bridges, roads, dams, and homes. Its durability, versatility, and affordability have made it the trusted choice for builders and engineers around the world.
Over time, many other types of cement have been developed and marketed as alternatives to portland cement. However, these alternative cements produce concrete with different properties, such as different setting times, expansive behavior, and altered strength development. These materials are used primarily for niche applications and have not gained broad traction in the market as a portland cement replacement.
The problem? Portland cement production comes at a massive climate cost. Traditional cement accounts for 7.5% of global CO₂ emissions—three times that of aviation and just behind cars.
Brimstone is working to change that. Our team has developed an efficient, economical and sustainable process to deliver conventional portland cement that meets existing industry standards (ASTM C150). We’re not changing the material itself—just the way it’s made—to seamlessly integrate into the production process, scale efficiently, and deliver cement that can secure a more sustainable future.
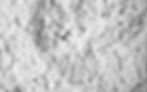
what is SCM?
Supplementary cementitious material (SCMs) are added to concrete to partially replace portland cement, improving its strength and durability while reducing its carbon footprint.
Common SCMs include ground granulated blast furnace slag and fly ash—materials typically sourced from coal-fired steel production or electricity generation. With the switch from blast furnaces to electric arc furnaces and the decline of coal-fired power plants, conventionally sourced SCM is becoming increasingly scarce. However, Brimstone has developed a solution.
Brimstone produces an SCM that meets existing standards and comes from a co-production process with ordinary portland cement—enabling these materials to reliably and seamlessly integrate into the construction supply chain.
One rock. One process. Two essential concrete ingredients.
our process
The Brimstone process produces two essential products used in concrete: portland cement and supplementary cementitious MATERIALs (SCM).
Cement and SCM are typically made through separate processes and sourced from different locations. Our rock contains all the necessary elements to produce both industry-standard cement and SCM from one process and in one location. Our process is deeply decarbonized across a range of energy scenarios.
we start with a carbon-free feedstock
TRADITIONAL CEMENT RELIES ON LIMESTONE AS ITS CORE FEEDSTOCK, WHICH ACCOUNTS FOR 60% OF CEMENT'S TOTAL EMISSIONS.
The Brimstone process replaces limestone with highly abundant and carbon-free calcium silicate rocks, dramatically reducing our cement's carbon footprint from the start.
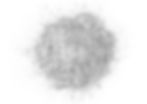
PORTLAND CEMENT
ASTM C150
Brimstone cement meets or exceeds ASTM C150 standards for portland cement, the most widely used cement in the world.
TRICALCIUM SILICATE CONTENT
>60%
28 DAY STRENGTH
>6000 PSI

SUPPLEMENTARY CEMENTITIOUS MATERIALS
ASTM C618 CLASS N
Brimstone SCM meets the physical and chemical requirements of ASTM C618 Class N.
r3 heat release
>200 J/g
28 DAY STRENGTH ACTIVITY INDEX
>100%
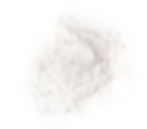
SMELTER GRADE ALUMINA
Industry specifications
Under development
ALUMINA CONTENT
>99%

step 1
geology
Portland cement is typically made from calcium and silica. Traditionally, this process involves heating limestone, which releases CO₂—about 60% of cement’s emissions come from heating limestone. The Brimstone process starts with a different feed rock: calcium silicates, which contain no embedded CO₂. Brimstone mines the feed rocks using a simple quarry operation and sends them to the lab.

step 2
mineral processing
A key part of the process is mineral processing, or comminution. During the comminution step, Brimstone crushes the feed rock to the desired particle size.

our process
The Brimstone process produces two essential products used in concrete: portland cement and supplementary cementitious MATERIALs (SCM).
Cement and SCM are typically made through separate processes and sourced from different locations. Our rock contains all the necessary elements to produce both industry-standard cement and SCM from one process and in one location. Our process is deeply decarbonized across a range of energy scenarios.
step 3
hydrometallurgy
Next, the Brimstone team mixes the calcium silicate rock with chemicals to extract calcium and other elements needed for cement production. These elements are separated to increase the calcium content to the level necessary for making portland cement. The remaining solid residue, rich in silica, becomes Brimstone's SCM material.

step 4
pyrometallurgy
Brimstone heats the extracted oxides in a rotary kiln to produce clinker, an intermediate product. The clinker is then milled with gypsum to create ordinary portland cement. Brimstone’s process is compatible with a wide range of energy scenarios, including clean energy.


©2024 Brimstone. All rights reserved.

PORTLAND CEMENT
ASTM C150
Brimstone cement meets or exceeds ASTM C 150 standards for portland cement, the most widely used cement in the world.
TRICALCIUM SILICATE CONTENT
>60%
28 DAY STRENGTH
>6000 PSI
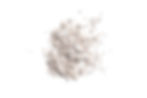.jpeg)
SUPPLEMENTARY CEMENTITIOUS MATERIALS (SCM)
ASTM C618 CLASS N
Brimstone SCM meets the physical and chemical requirements of ASTM C618 Class N.
r3 cumulative heat release
>200 J/g of SCM
28 DAY STRENGTH ACTIVITY
>100%
step 1
geology
Portland cement is typically made from calcium and silica. Traditionally, this process involves heating limestone, which releases CO₂—about 60% of cement’s emissions come from heating limestone. The Brimstone process starts with a different feed rock: calcium silicates, which contain no embedded CO₂. Brimstone mines the feed rocks using a simple quarry operation and sends them to the lab.

step 2
mineral processing
A key part of the process is mineral processing, or comminution. During the comminution step, Brimstone crushes the feed rock to the desired particle size.

step 3
hydrometallurgy
Next, the Brimstone team mixes the calcium silicate rock with chemicals to extract calcium and other elements needed for cement production. These elements are separated to increase the calcium content to the level necessary for making portland cement. The remaining solid residue, rich in silica, becomes Brimstone's SCM material.

step 4
pyrometallurgy
Brimstone heats the extracted oxides in a rotary kiln to produce clinker, an intermediate product. The clinker is then milled with gypsum to create ordinary portland cement. Brimstone’s process is compatible with a wide range of energy scenarios, including clean energy.

